Riding The Waves
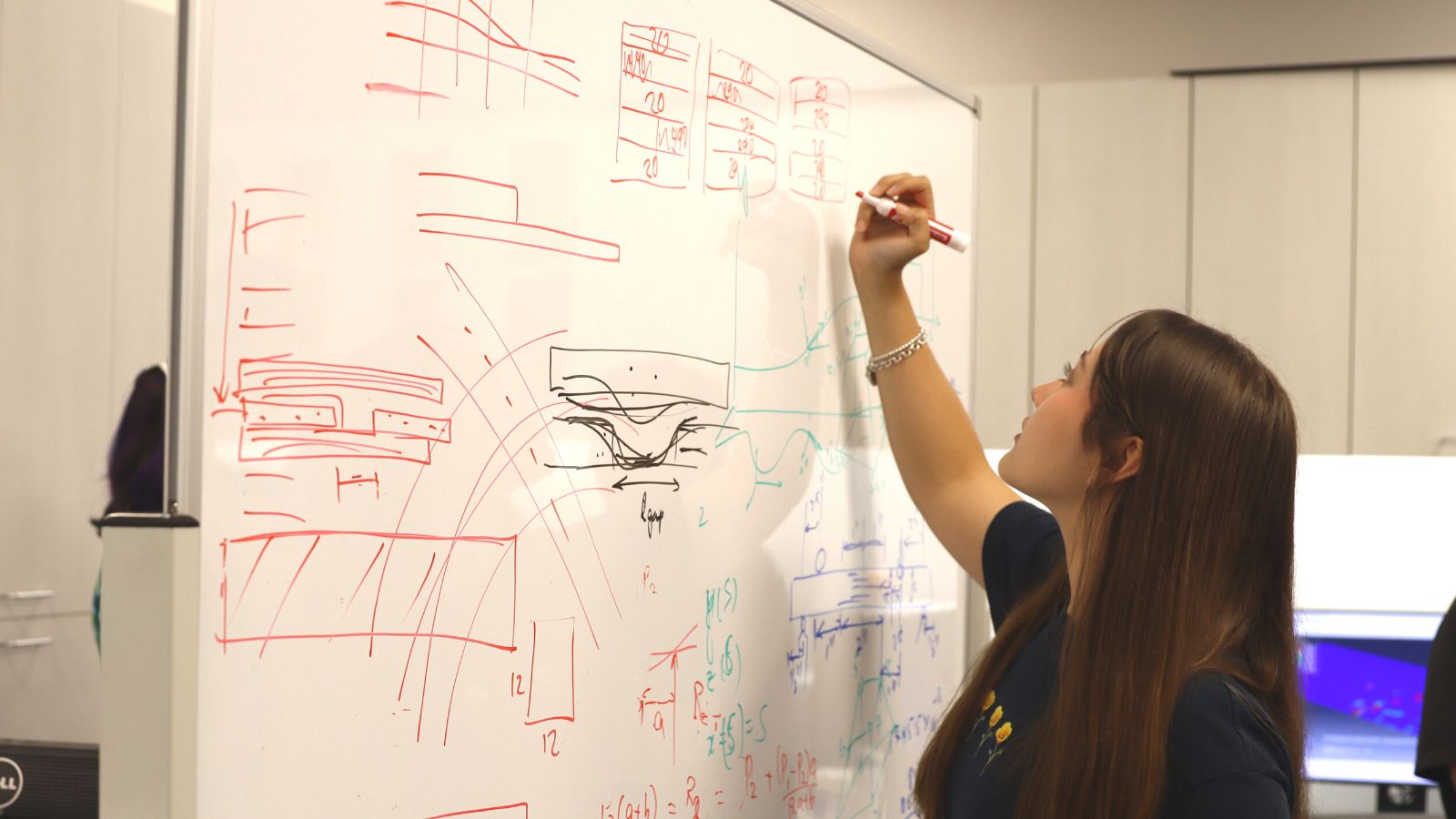
SDSU undergraduate researcher Gabriela Gonzalez Ayala works in Dr. Venkataraman's aerospace engineering lab on characterizing the geometry of a defect in carbon fiber-reinforced materials called ply waviness.
What were the goals of the project that you worked on?
The goal of my personal summer project was to create panels with ply waviness, characterize their geometry and collect experimental data performing tension tests. The goal of my project was to collect experimental data and information about ply waviness geometry. This information will be used to validate FEA models and make them more reliable.
Why is this research important and interesting?
Composite materials are used a lot in the aerospace industry. Carbon fiber reinforced polymer (CFRP) parts are particularly known for being much lighter, stronger, and stiffer than most other metals used in aircraft structures. There are several ways in which these CFRP parts are made, they are usually very labor intensive and expensive. However, there is a manufacturing process called Automated Fiber Placement (AFP) in which a robotic arm lays down and cures tows of CFRP onto molds. This process allows for the making of very intricate parts called tailored composites. However, this system is not perfect and when you have double curved areas the tows may not line up perfectly. As more layers are added to the part we see the creation of gaps and overlaps of tows, and in turn, this leads to uneven changes in thickness and ply waviness. We still don’t really understand how the waviness in the plies affects the mechanical properties of the part. However, studying the effect that ply waviness has is very important. It’s important to test these parts with ply waviness under tension, compression, fatigue, etc. Ply waviness is a manufacturing error that can’t really be avoided but understanding how failure initiates and progresses in these parts will make maintenance of parts more efficient, among other things.
What were some of the tasks you worked on?
I made two 12”x12” carbon fiber panels with ply waviness in them. I cut the panels up into 10”x1” test specimens. I polished the cross section and did microscopy on one inch of the specimen, specifically the area around the ply waviness. The picture I am looking at on the monitor is a 100x magnification of the actual specimen which is ~2mm in thickness. That image allowed me to measure waviness amplitude, waviness length, specimen thickness, individual ply thickness, among other things that will allow me to characterize the specimen.
What did you enjoy most about working in the lab and doing research? What I enjoyed most about working in the lab and doing research was discovering a new environment where I could grow as a student. I enjoyed discovering a dynamic where I’m working with a team that’s trying to reach the same goal, and every person is solving a different aspect of the goal, as they rarely are simple projects. I enjoy knowing that even though I didn’t make any revolutionary discoveries over those 10 weeks, my work will help further someone else’s research. The idea of leaving even a small mark on this field of research was very fulfilling for me.
What skills have you gained from working on the project?
I’ve learned many technical skills: I know how to make CFRP panels using pre-preg; I learned how to use equipment like a tile saw, a hot press, and an INSTRON machine; and I learned to use software like MATLAB, and even a bit of ABAQUS. I also developed several soft skills: I improved my public speaking skills as I was presenting updates to my colleagues every week, as well as having a final presentation; I became a better planner as I had to coordinate layups, test specimen fabrication, etc; and I became more inquisitive as I started to ask myself more questions every time I came across a hurdle during my research trying to see what piece of the puzzle I was missing.
Learn more about the lab here. View more photos of the lab here.